Worker Fatigue

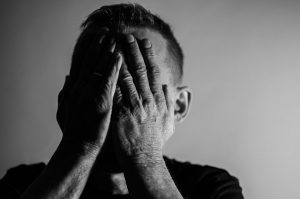
According to the Centers for Disease Control and Prevention (CDC), nearly 15 million Americans work irregular schedules, including full-time evening shifts, night shifts, and rotating shifts. These kinds of shifts have been associated with safety and health risks, and certain jobs are at higher risk. It is important that both employers and employees are educated on worker fatigue risks to keep their workplace safe and running smoothly.
What Causes It?
There are several factors that cause worker fatigue, including too little or poor quality sleep over a period of time. This is also known as a disrupted circadian rhythm. A circadian rhythm is a 24-hour, internal cycle that controls when you feel alert and when you feel sleepy. Fatigue can also be intensified by long work hours or insufficient rest during the workday.
Industries that are commonly affected by worker fatigue include healthcare, transportation, first response, military, construction, hospitality, and many others.
The Side Effects
It is hard for the body to acclimate to changing/irregular schedules. Along with increased stress and lack of concentration, the side effects of worker fatigue may include:
- Increased chance that you will not pay full attention to the task at hand, such as operating a machine or a vehicle. This can lead to even larger disasters on the job.
- Increased risk of injuries. Research indicates that working 12 hours per day is associated with a 37% increased risk of injury.
- Decreased physical and mental health, which may result in greater time off the job due to illness and increased workers’ compensation costs for the employer.
How to Improve It
- Moderate your workload as much as possible. If shifts are long, try to choose lighter tasks. If the work is intense, try to work shorter shifts.
- Eat nutritious meals at regular times.
- For demanding work, take frequent rest breaks every couple of hours.
- Exercise regularly if you can, even a brisk walk can make all the difference.
- Schedule heavy or challenging work at times when you are more alert to decrease the risk of an accident.
- Adjust lighting or temperature (or request that they are adjusted) if either is impairing your alertness at work.
- Get at least 7-9 hours of uninterrupted sleep. This is the recommended amount of sleep for adults from the National Sleep Foundation.
If you any questions regarding worker fatigue, feel free to contact our Risk Management Coordinator, Ryan Wilson at 802-295-3329 or [email protected]
For more information, check out these additional resources:
https://www.osha.gov/SLTC/workerfatigue/hazards.html
https://www.nsc.org/work-safety/safety-topics/fatigue
http://www.safetynewsalert.com/10-workplace-fatigue-hazards/
Article written by: Ryan Wilson
DISCLAIMER:
The information included in this publication and accompanying materials was obtained from sources believed to be reliable for informational purposes only. Northern Safety Solutions/Kinney Pike Insurance and its employees make no guarantee of results in connection with any training, materials, suggestions, or information provided. This information is only a tool to assist you in managing your responsibility to maintain safe premises, practices, operations, and equipment. All sample materials serve as a guideline, which you can use to create your own programs, policies, and procedures to reflect your own operations. Furthermore, it cannot be assumed that all possible hazardous conditions or unsafe acts that may exist are covered, every acceptable safety method is contained in this publication, or that specific circumstance may not require additional methods or alternative safety considerations. It is the user’s responsibility to confirm compliance with any applicable local, state or federal regulations. Information obtained from or via Northern Safety Solutions/Kinney Pike Insurance should not be used as the basis for legal advice or other advice, and should be confirmed with alternative sources. Implementation of any practices suggested by this information is at your sole discretion; and Northern Safety Solutions / Kinney Pike Insurance or its affiliates shall not be liable to any party for any damages whatsoever arising out of, or in connection with, the information provided or its use.